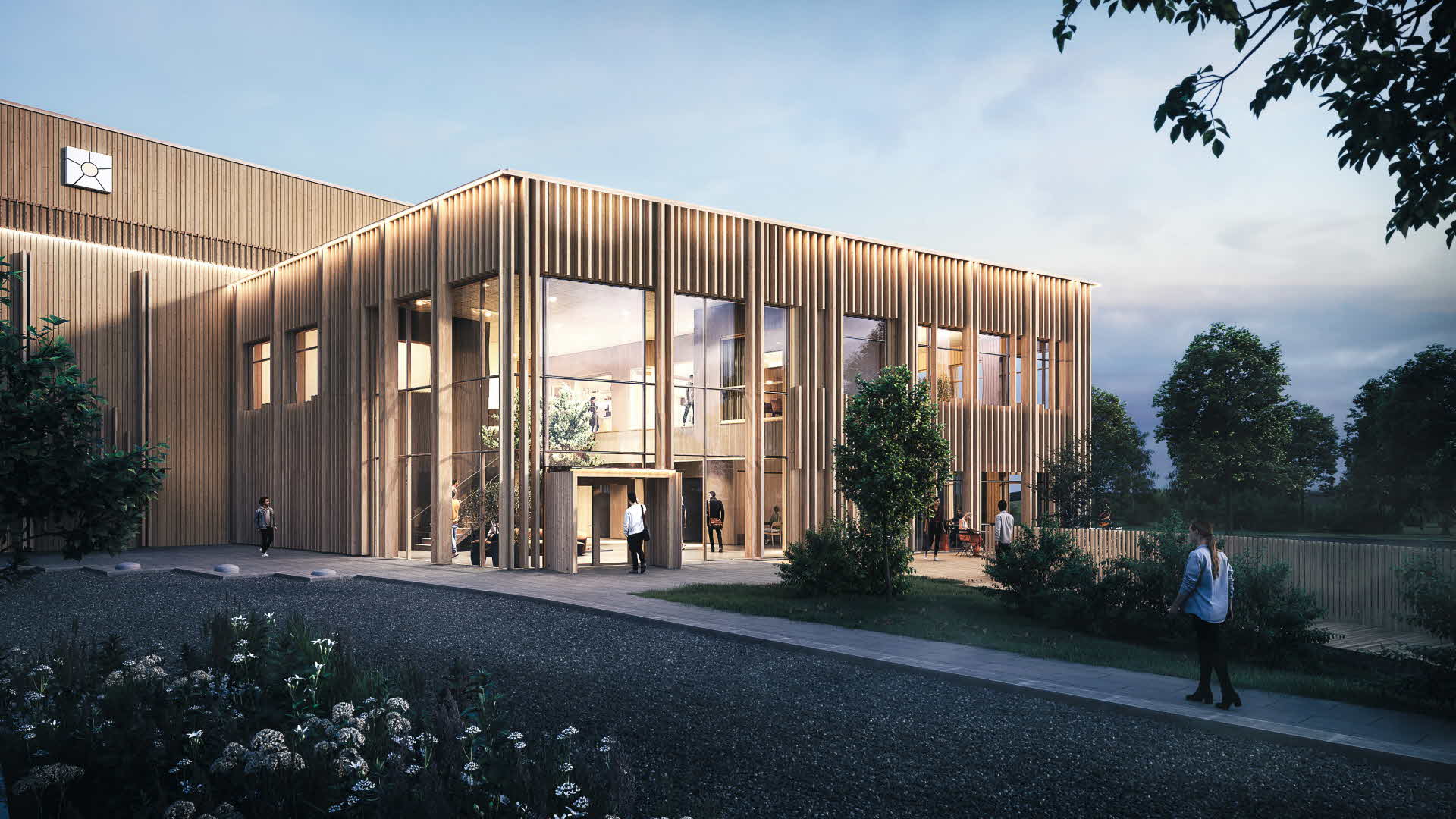
- WOOD
- INNOVATIVE TIMBER PROJECT DRIVE CONSTRUCTION INDUSTRY FORWARD
Timber project drive construction industry forward
- Article
Fifty kilometres outside Stockholm, in the small town of Bålsta, something is happening that’s never been done before, and that nobody really knows how to do as yet. Not even Logicenters, which will be implementing the project. And yet the company is working on erecting the world’s first carbon-free logistics hall. A massive building, more than 20,000 square metres in area and made almost entirely of timber, which will produce no emissions at all during its life-cycle.
The property sector´s carbon footprint is too big to ignore. Properties account for 40 per cent of global emissions overall. This is an industry in dire need of better ways to develop and manage properties. We’re determined to lead the way towards a carbon-neutral sector,” says Eva Sterner, head of project development at Logicenters, NREP’s logistics arm.
To say that the company is setting the bar high would be something of an understatement. Its entire property portfolio will be carbon-neutral by 2028. This is an ambitious target that sounds almost impossible to achieve, given the current situation where the construction industry’s carbon dioxide emissions are some of the highest in the world. At least, they are if you’re not prepared to take a chance.
“The objective set out by Logicenters was to achieve the longest possible maintenance interval, and to ensure that nothing would need to be done for at least 25 years. This objective can only really be achieved sustainably by using core pine panelling. Or, in other words, panels made from the innermost part of the tree. The part that’s been allowed to grow for the longest time, and that’s so dense that it’s naturally impregnated,” says Anders Petersson, director of innovation and sustainability at SCA Wood.
“At Logicenters, we’re now exploring and implementing an initial innovation project with a high level of ambition and a clear aim to benefit our planet,” says Eva Sterner.
“We hope our Bålsta project will serve as a guide on how buildings can be designed, built and managed in a carbon-neutral way. We’re committed to openly sharing insights, mistakes and lessons learned as we work on achieving this,” she continues.
Three groundbreaking projects
So the ambition with the logistics hall in Bålsta is to rethink and start thinking along new lines. To create a new standard for developing buildings on the basis of three key objectives. Net zero embodied carbon dioxide, net zero operational carbon dioxide, and net zero additional costs. Eva admits that this would be difficult to achieve today, but they believe they’ve come a long way towards this goal thanks to extensive research and a great deal of risk-taking.
“To be honest, it’s a bit harder to do this without it costing more. Until there are more economies of scale with carbon-friendly materials and technologies, they come at an additional cost, at least at the moment. But based on what we’ve seen, we’re expect to see a green economic upside in this project. We’re already seeing some strong interest in the project from banks from a funding perspective, and also from potential tenants who are wanting to relocate to this groundbreaking facility. That’s why we remain convinced that overall, this project will be particularly attractive from a commercial standpoint and therefore also ‘zero’ in terms of net cost.”
“We’re working with leading innovators in the industry to push the boundaries and deliver the world’s greenest logistics developments. Working on the basis of the most advanced products available, this project will provide a test bed for new solutions with a view to creating a whole new commercially viable paradigm when it comes to carbon-neutral buildings,” continues Eva.
Maintenance-free core pine façade
One of these innovators is SCA Wood, which encountered the project through other research commitments. It’s played an advisory role during the preparation phase, not least as regards the façade, and when the facility is finished it’ll be clad entirely in the company’s highest quality façade panelling, which is made from 99 per cent core pine.
“The objective set out by Logicenters was to achieve the longest possible maintenance interval, and to ensure that nothing would need to be done for at least 25 years. This objective can only really be achieved sustainably by using core pine panelling. Or, in other words, panels made from the innermost part of the tree. The part that’s been allowed to grow for the longest time, and that’s so dense that it’s naturally impregnated,” says Anders Petersson, director of innovation and sustainability at SCA Wood.
In turn, the structure and the supporting elements, which will also be made entirely of wood, will be supplied by Holmen and Martinson. The roof will be covered by solar panels, which will provide all the electricity needed by the facility in combination with battery storage. This will make it possible to regulate peak demand from equipment and vehicles, as well as feeding surplus electricity back to the grid. “We’ll be exploring various decommissioning options and future new solutions so that we can reduce emissions still further going forward. As this building is likely to be decommissioned in over 50 years’ time, we’re confident that even more solutions will be available by then,” concludes Eva.