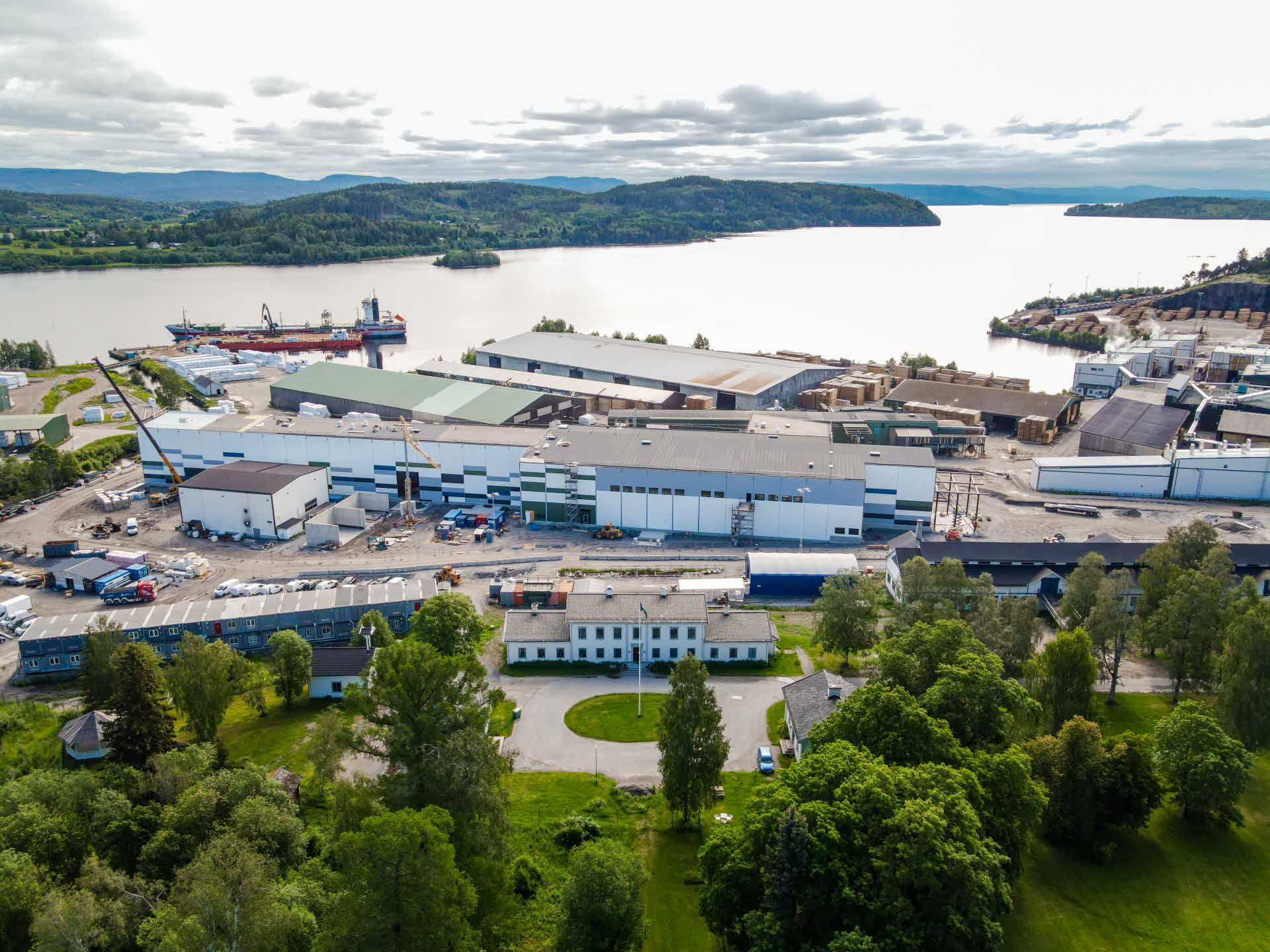
Prepared to meet the future
- News
- Wood products
The word digitisation immediately brings to mind massive server halls full of blinking lights, e-invoices and digital meetings. Likewise, we tend to associate industry with heavy machinery, assembly lines and manual labour. A somewhat outdated image that no longer entirely reflects reality. Not in Bollsta, at least. It is there that one of the most technologically advanced dry sorting lines in the world is currently being installed; a smart facility that will only grow smarter as time goes by.
T HE SOUND OF HAMMERS striking metal and builders loudly communicating with one another between floors creates a hectic atmosphere. There is a hive of activity almost everywhere one looks in the 200-metre-long building that will soon house one of the world’s most advanced dry sorting lines.
“There are a lot of us in here right now but once we’re up and running the entire facility and all the machines will only require three operators,” says Johan Olofsson, Technology & Operation Excellence Manager at SCA Wood.
It is barely two years since Johan and his colleagues on the B700 project, as it has been designated internally, witnessed the foundations of the new building being poured and begin work in earnest. A great deal has happened since then, within the project and in the world at large.
“If someone had told me in November 2019 that we were facing a pandemic I would probably have found it difficult to be optimistic; I think anyone would have. The advantage we have, which I think contributed to managing to stay on schedule, is that we had already made a start. Much of what we needed was already on site here in Bollsta and we were able to keep working as the countries of the world locked down,” says Johan.
Of course, it is no coincidence that within SCA the project has been designated with the number 700; once the new state.of-the-art technology, robots and other digital tools are installed, the new dry sorting line will help to increase the sawmill’s total annual production capacity to approximately 700,000 cubic metres of sawn timber products. This is a significant increase that in turn will enable the business in Bollsta – which currently produces 550,000 cubic metres of sawn timber products annually – to continue to enjoy long-term growth going forward.
“As in all other parts of society, we see enormous potential in further digitising our processes. The art of sawing timber is hardly new; on the contrary, we have been trying to refine our work for centuries,” says Johan.
“However, if we are to successfully take the next step on the journey and really maximise the value of every millimetre we saw, we will also need to be more digital. We need to take full advantage of the technical aids we have at our disposal today while simultaneously equipping ourselves for what we believe will be possible tomorrow.”
Log x-rays and 3D models
One obvious example highlighted by Johan is the computed tomography (CT) scanner installed at Bollsta last year as part of the project. An advanced type of X-ray equipment, similar to the scanners used in hospitals to examine patients, can produce three-dimensional images of logs, revealing their internal characteristics.
“The logs we saw will often have stood in the forest growing for between 70 and 100 years. The fact that we can now see straight through them is a real game-changer. We obtain much more valuable data to go on, making it easier to use the right log for the right product and ultimately get more from less,” continues Johan.
Where once it was only possible to judge how to saw a log based on its exterior characteristics and shape, using the new technology at Bollsta and the images it produces, it is now possible to see inside the logs. In other words, no longer need anything be left to chance.
“The CT scanner is a highly illustrative example of what we are trying to achieve. We intend to have the very latest equipment and the best available aids that can give us a competitive edge here and now but that will not fulfil their full potential for some time to come. Eventually, we will be able to connect all of the data we obtain now through the CT scanner with other data from the plant. We know this, but what data and what we can learn from it remains to be seen,” says Johan.
Virtual production lines and machine learning
Seemingly endless cords snake down beneath the floor or up to the ceiling from every machine in this crammed building. Some terminate in the facility’s electrical panels while others will be connected directly to computers.
“The idea is that we will be able to run a virtual version of the dry sorting line in parallel with the real thing, both so that we can easily rewind at our leisure to follow up any problems that may arise, but also so we can identify patterns in how we work, “ explains Johan, who concludes:
“Eventually, a computer that has watched an operator fix a given problem in the same way many times will be able to suggest solutions much more quickly and, ultimately, even fix the problem itself as and when it arises. Machine learning might not be the top priority right now but, as I said, it is equally important that we are prepared for whatever the future holds.”